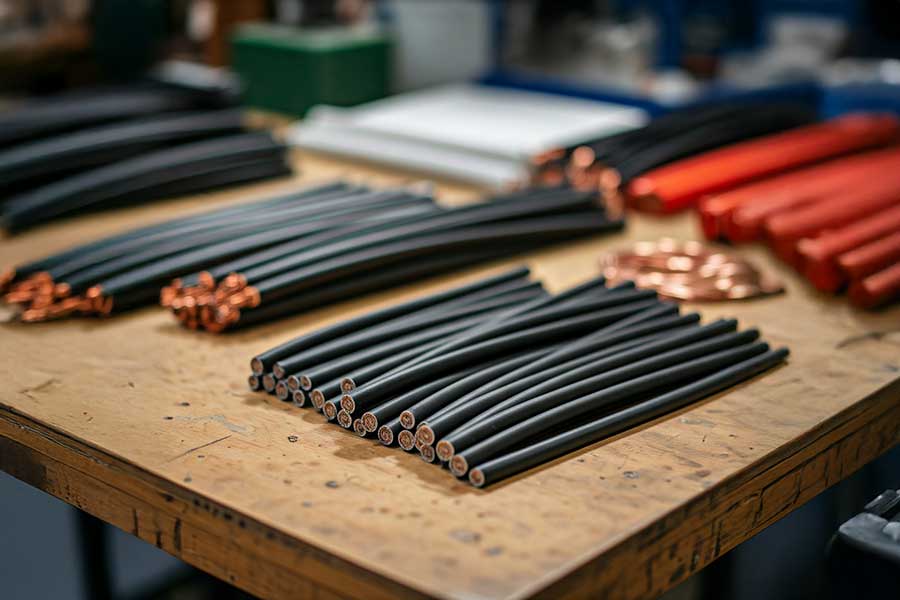
Cables used to safely and efficiently transmit electrical energy from one point to another are an indispensable part of the modern world. Although they may seem like simple fastening tools, they go through a complex manufacturing process and are made from a variety of materials to suit different applications. As Ülkü Kablo, we are constantly improving our production processes and the technologies we use and aim to be the top in cable production. In this text, we will examine the cable manufacturing process step by step and take a closer look at the main materials used in cable construction.
Cable Production Process
Cable production consists of several basic stages:
- Wire Drawing: The metal (usually copper or aluminum) rods to be used as conductors are passed through a series of molds to be thinned and brought to the desired diameter. This process is called "wire pulling". The wire drawing process improves the mechanical properties of the metal and increases its conductivity.
- Vein Formation: Thin wires are brought together in the desired number to form a "vein". Veins can be single-stranded or stranded. Multi-stranded cores give the cable more flexibility.
- Insulation: The veins are covered with an insulating material to prevent the leakage of electric current to the outside. The insulating material is selected according to the intended use of the cable and its operating voltage.
- Twisting (Core Twisting): In multi-core cables, insulated cores are twisted together. This process imparts mechanical strength to the cable and reduces electromagnetic interference.
- Inner Sheath (Padding): The twisted cores can be covered with a padding material to fill in the gaps and give the cable a rounded shape. This process is called "inner sheath" or "filling".
- Armoring (If Required): In cases where the cable needs to be protected against mechanical impact, rodents, or other external factors, a metal armor can be applied to the cable. Armor usually consists of steel wires or strips.
- Outer Sheath: It is the outermost layer that protects the cable against environmental influences (moisture, UV rays, chemicals, etc.). The outer sheath material is selected according to the area of use of the cable and the conditions to which it will be exposed.
- Testing and Quality Control: At each stage and end of the production process, various tests are performed to check the electrical, mechanical, and environmental properties of the cables.
Main Materials Used in Cable Construction
The materials used in cable construction directly affect the performance, durability, and safety of the cable. The main materials used are:
- Conductors:
- Copper: It is the most widely used conductive material. It is preferred due to its high conductivity, corrosion resistance and easy machinability.
- Aluminum: It is lighter and cheaper than copper. However, its conductivity is lower than that of copper. It is used in high voltage lines and some power cables.
- Copper Alloys: Copper alloys (beryllium copper, cadmium copper, etc.) can be used for special applications (e.g., high temperature or high frequency applications).
- Insulation Materials:
- PVC (Polyvinyl Chloride): It is the most widely used insulation material. It is preferred due to its low cost, good electrical properties and easy machinability.
- PE (Polyethylene): It has better electrical properties and higher temperature resistance. It is used in high voltage cables and communication cables.
- XLPE (Cross-Linked Polyethylene): It has higher temperature resistance and better mechanical properties than PE. It is used in medium and high voltage cables.
- Rubber (Silicone Rubber, EPR, etc.): It has high flexibility, high temperature resistance and good electrical properties. It is used in special applications (e.g., high temperature or moving applications).
- Sheath Materials:
- PVC: It is the most widely used sheath material. It is preferred due to its low cost, good mechanical properties and flame retardancy.
- PE: Provides better environmental resistance and UV resistance. It is used in outdoor cables.
- PUR (Polyurethane): Provides high abrasion, chemical and mechanical resistance. It is used in specialized applications (for example, robotics or mining).
- Halogen Free Materials: These are special materials that do not emit toxic gases in case of fire. It is used in buildings with high human density and in places where fire safety is critical.
Cable Standards
Cable production is carried out in accordance with international and national standards (for example, IEC, EN, TS). These standards determine the electrical, mechanical and environmental properties of cables and ensure their safe use.
Result
Cable production is a complex process with the selection of raw materials, the control of production processes and the implementation of quality tests. Choosing the right material and proper manufacturing techniques directly affect the performance, reliability and life of the cables. Therefore, when choosing a cable, it is important to consider the requirements of the application and the relevant standards. We are at your service with our production processes in accordance with all necessary standards.