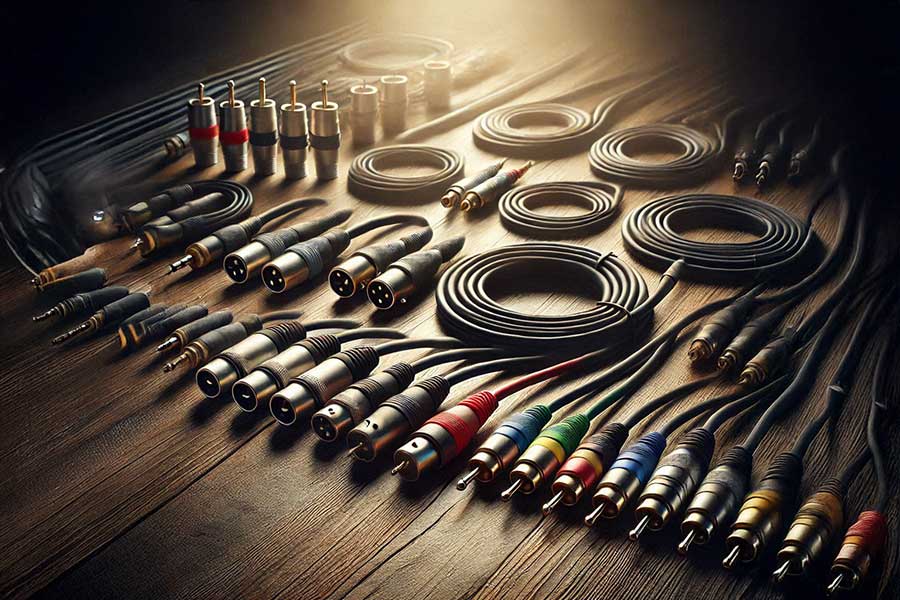
Audio cables are the invisible heroes of audio systems. Whether you're listening to music, watching movies, or recording in the studio, they play a critical role in a seamless audio experience. However, the production of these seemingly simple components presents a number of technical and practical challenges. So, what challenges do audio cable manufacturers face during their production phases?
1. High Quality Material Sourcing and Control is the Key Element of Manufacturing and Quality.
- Purity of Conductive Materials: Conductors such as high-purity copper (such as OFC, OCC) or silver are used to transmit the audio signal with minimal loss. The sourcing of these metals and the control of their purity grade is a significant challenge for manufacturers. Price fluctuations and supply chain issues, especially of rare metals, can affect production.
- Selection and Performance of Insulation Materials: Insulation materials are critical for signal protection and interference prevention. Different insulation materials (PVC, PE, Teflon, etc.) differ in their dielectric properties, flexibility and durability. Manufacturers have to choose the most suitable insulation material for the application area and test its performance.
- Connector Quality and Compatibility: Connectors can be the weakest link in the cable. Procurement, installation and compatibility of quality connectors with the cable is an important issue for manufacturers. The mechanical strength, contact resistance and signal transmission performance of the connectors should be tested.
2. Precision manufacturing processes in cable production:
- Cable Pulling and Bending: Precise pulling of thin wires and twisting the desired number of wires together requires special machines and expertise. It is important that the wires do not break, that they are twisted in equal tension and that the cable geometry is maintained.
- Insulation and Shielding: Insulating and shielding conductors is a critical stage to protect the signal and prevent it from being affected by external factors. Homogeneous application of the insulation material, effective shielding and maintaining cable flexibility can create challenges.
- Connector Assembly and Soldering: Correctly mounting and soldering connectors to the cable is critical to signal transmission and mechanical durability. The quality of the solder, contact resistance and joint strength must be tested.
3. Kinds of cable quality control & Testing:
- Electrical Tests: It is necessary to measure the electrical properties (resistance, capacitance, inductance, impedance, etc.) of the produced cables and check their compliance with the standards. These tests require special testing equipment and expertise.
- Mechanical Tests: Testing the mechanical strength (pulling, bending, impact, etc.) of the cables is important to prevent damage that may occur during use.
- Environmental Tests: Testing the resistance of cables to different environmental conditions (temperature, humidity, UV rays, etc.) is essential to provide long-lasting and reliable products.
4. Cable Production Costs and Competition:
- Raw Material Prices: Fluctuations in the prices of metals such as copper and silver can affect production costs and make competitiveness difficult.
- Labor and Energy Costs: Labor and energy costs in production processes are also factors that affect the total cost.
- Competitive Environment: There are many audio cable manufacturers in the market. Offering competitive prices and maintaining high quality at the same time is a key challenge for manufacturers.
After all:
Audio cable manufacturing involves many challenges, from material selection to manufacturing processes, from quality control to cost management. Manufacturers must have the technical know-how, expertise, modern production facilities, and stringent quality control processes to meet these challenges. This allows them to produce high-quality audio cables that provide music lovers, sound technicians, and studios with a seamless audio experience.